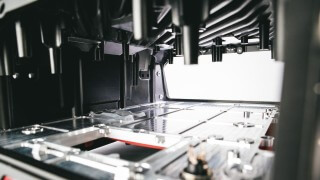
Expertise
DESIGN FOR MANUFACTURING EXPERTS
Advanta mechanical design skills, plus a desire for learning over many years helped us gather expertise on many production methods. We have the experience to correctly design for each production technology and provide vendors precisely the files these need to make excellent parts. With every new project a little more expertise from each supplier rubs off on us.
-
Move Forward Confidently with Our Guidance
We aim to be your trusted guide throughout the product development journey. By steering our clients through the process, we empower them to make informed decisions. We elucidate the challenges, enabling them to actively participate in the decision-making process and ensure the success of their product.
We Can Review Your Current Design, Even if we did not design it
Whether your team has advanced in product design or if another design group created your product, we can assist in uncovering potential pitfalls and enhancements. Consider us for a second opinion before investing in costly production tooling. Many of our clients initially sought assistance as entrepreneurs, seeking to review or rectify designs created by other design teams.
-
Mastering 3D CAD
Our expertise lies in crafting intricate surface models, multi-part assemblies, and complex mechanical systems. We translate intricate concept sketches into tangible products, preserving design integrity at every step.
Manufacturing Expertise
Look no further; our in-house experts offer guidance on material selection, manufacturing processes, and connect you with qualified local or offshore manufacturers at your convenience.
Design A to Z, from Idea to Production
We provide comprehensive support from ideation to final product delivery, offering strategic direction, assistance, and connections to turn your ideas into reality with both 2D and 3D production files.
WHAT WE DESIGN
With years of collective experience, our expansive team has honed its expertise in designing electronic enclosures, rugged performance products, furniture, laboratory and medical devices, and transportation solutions. Having successfully designed over 350 products, we possess a deep understanding of diverse industries and are well-equipped to tackle a wide range of design challenges with precision and innovation. We are used to applying our knowledge cross-market innovation in design and manufacturing solutions.
-
HAND IN HAND WITH YOUR ELECTRONIC TEAM
Our team possess an extensive knowledge for integrating electronics and circuit boards into enclosures of all sorts. Our expertise ensures proper fit, thermal management, communication protocol specificity and protection from environmental factors, enabling us to design functional and reliable products that meet performance requirements and user expectations.
HEAT DISSIPATION DESIGNOur mechanical design team excels in designing electronic enclosures for effective heat management. Key considerations include airflow optimization, thermal insulation, material selection for heat dissipation, provision of adequate ventilation, and integration of heat sinks or fans to maintain optimal operating temperatures.
HAND HELD DEVICES
We prioritize UX design for handheld products, understanding the importance of user interaction. Key considerations include ergonomic grip, intuitive button placement, tactile feedback, weight distribution, and ensuring comfort during prolonged use without compromising on durability, aesthetics, and ease of maintenance. All to enhance overall user experience.
GPS AND SIGNAL PERMEABILITY
GPS electronic enclosures are challenging to design because you need to consider signal transparency, antenna placement, and electromagnetic shielding while upholding enclosure integrity. Our team has extensive knowledge and experience doing so.
FLAME RETARDANT (V0) AND ANTI-STATIC MATERIALS
When designing enclosures with fire and flame retardant plastic, prioritize UL V0 plastics for high fire resistance. Incorporate anti-static materials to prevent static buildup. Ensure compliance with safety standards and regulations. Conduct thorough testing to verify flame resistance and anti-static properties, ensuring product safety and reliability.
EMI RMI SCHIELDING
Beware when designing enclosures with EMI and RFI shielding needs. We must pay close attention to material conductivity, enclosure geometry for field containment, and the inclusion of tight gaskets or seals. Use shielding layers appropriately and ensure strict adherence to standards. Rigorous testing will be imperative to validate shielding effectiveness.
-
WATER INGRESS PROTECTION IP 65, IP 66, IP 67
As an experienced design team, we've engineered numerous sealed products, comprehending the importance of water ingress protection and IP ratings. Challenges in our design process entail sealing vulnerable areas, material selection, and striking a balance between protection and functionality, all informed by our extensive experience. Achieving higher IP ratings often requires trade-offs in cost, product size, and complexity.
IMPACT & DROP TESTING
Drop testing, including impact resistance, is crucial for products facing rugged conditions, ensuring safety and functionality. By simulating real-world scenarios, it assesses a product's resistance to impact at every angle, validating its durability. This testing could be essential for meeting certification and standards and instilling confidence for users regarding product reliability under harsh daily use.
CYCLING & TESTING
Product cycling testing involves subjecting a product to repeated cycles of operation or stress to assess its durability and performance over time. This testing simulates real-world usage conditions, helping to identify potential failures or weaknesses and ensuring the product meets reliability and quality standards. It is crucial in designing rugged, reliable products that withstand prolonged use.
CERTIFICATION ANC COMPLIANCE
Clients often underestimate the importance of certifications and standards, believing they're irrelevant to their products. Yet, certified products provide assurance of safety and compliance. Failure to comply can result in limitations on product use and indirectly impact sales. While it requires time and investment, we'll guide you through the process and connect you with trusted conformity assessment partners who have supported us in numerous design projects, ensuring adherence to standards and regulations.
EXPLOSION PROOF AND INTRINSICALLY SAFE
Designing explosion-proof and intrinsically safe products involves ensuring that they are constructed to prevent ignition of hazardous materials in explosive atmospheres. This includes using specialized enclosures, seals, and materials to contain any potential sparks or heat generated by the device, thus minimizing the risk of explosion. We have the knowledge and experience to design your product.
-
HIGH VALUE LOW VOLUME
A high-value, low-volume product is one that commands a premium price due to its unique features, technology, or exclusivity but is produced in relatively small quantities. These products cater to niche markets or specialized needs, offering exceptional quality and often customization options.
SECURITY AND SAFETY
Security and safety devices are a multifunctional equipment designed to enhance user security, ensure safety protocols, and monitor assets in industrial and tough environments. These devices encompass features like rugged enclosure, communication systems, access control systems, emergency alarms, and tracking technologies, enabling comprehensive monitoring and management of operational risks and resources.
INSPECTION, MONITORING & NDT
Field Ready Inspection, monitoring, and NDT (Non-Destructive Testing) devices are specialized equipment used to assess the integrity, quality, and performance of materials, structures, and components in various industries. These devices include sensors, cameras, and testing tools, enabling accurate evaluation without causing damage, ensuring safety and compliance standards are met.
INDUSTRIAL PRODUCTS
The high-end machinery sector greatly benefits from industrial design expertise in optimizing product functionality, usability, and aesthetics to stand out from competitors. Prioritizing user-centric design and innovation distinguishes industrial machines, ensuring customer satisfaction, loyalty, and competitive advantage. Regrettably, it remains a market that does not always see the value industrial design can bring.
AGRICULTURE PRODUCTS
A high-tech agricultural product incorporates advanced technologies and innovations to improve farming efficiency, productivity, and sustainability. These products encompass precision farming tools, smart sensors, drones, and automated machinery, revolutionizing traditional agricultural practices and addressing modern challenges in food production and environmental conservation.
LAB AND MEDICAL
Precision, sanitation, repeatability and usability pose design challenges. Quality mechanical design requires thorough testing, regulatory compliance, and collaboration among designers, engineers, and science specialists. This ensures reliable, accurate equipment with user-friendly interfaces, improving patient care and streamlining tools for advancing science and medical research.
PROTOTYPING
In the realm of industrial design, prototype manufacturing holds a pivotal role, offering our clients an invaluable opportunity to save resources and enhance product outcomes. By investing in these prototypes, we can uncover potential design flaws before mass production, mitigating costly errors and minimizing financial risks. They are power full learning tools. Additionally, iterative prototyping facilitates fine-tuning product features, ensuring optimal performance and customer satisfaction. Ultimately, embracing prototype manufacturing empowers your design team to craft superior products while maximizing efficiency and profitability in the long run.
-
P0
A P0, also known as Prototype 0, validates the essential ergonomics and technical functionality of a product. It concentrates on refining core features, while visual aesthetics are handled in early sketches and CAD models. This initial prototype aims solely to ensure effective and comfortable functionality, laying the foundation for subsequent design iterations where aesthetic concerns take precedence. Often, our clients provide us with a P0 crafted by their engineering team as a starting point.
P1
A P1, or Prototype 1, showcases the ergonomics, form, and detailed functionality/performance of the final product. While it doesn't undergo reliability and durability testing, it allows for validation of specific sections or mechanisms rather than the entire product. This prototype serves to refine design elements and ensure that the product meets performance expectations, laying the groundwork for further refinement and eventual production.
P2 (ALPHA)
The P2, or Prototype 2, mirrors the functionalities of P1 but with finalized detailing. Materials and assembly closely resemble those intended for production. These prototypes could undergo rigorous endurance testing, simulating real-world conditions to ensure product durability and reliability. Often termed as the ALPHA build, this stage marks a significant milestone where the product's design and performance are thoroughly scrutinized before moving towards mass production, providing valuable insights for further refinement.
P3 (BETA)
The P3 represents a full-production product fabricated in a controlled laboratory setting. It adheres strictly to production intent, encompassing materials, colors, and assembly methods, employing production tooling. Although sometimes lacking in-mold texturing or product graphics, this prototype undergoes comprehensive endurance and certification testing. Often termed as the BETA build, this stage marks a pivotal step where the product is evaluated under real-world conditions, ensuring it meets quality standards and regulatory requirements before final production and market release.
-
UX, ERGONOMICAL PROTOTYPE
Prototyping in industrial design is vital for optimizing user experience and ergonomics. Through iterative testing, designers refine product features to ensure usability and comfort. This iterative process allows for the creation of products that not only meet user needs but also enhance their overall satisfaction and usability.
FAIL FAST
Creating iterative, quick, functional prototypes is vital in product design for rapid learning and failure. It allows designers to test ideas, identify flaws early, and iterate swiftly, fostering innovation while minimizing time and cost. This iterative process accelerates learning, leading to more robust and successful final products.
FULL-SCALE LARGE PROTOTYPE
Crafting large prototypes such as agricultural machinery, walk-in trains cabins or furniture demand careful planning and execution. It's vital to experiment with real-size proportions and user interactions, as opposed to relying solely on screen-based 3D models limited to around 21" wide, to ensure a thorough evaluation of usability and potential risks.
FIELD TESTING
Prototyping for field testing products is crucial for evaluating real-world performance and gathering user feedback. By testing prototypes in actual environments, designers can identify and address issues before it is too late and engaging high production cost. It serves as a test to validate that final products meet user needs, perform reliably, and excel in various conditions as expected and designed.
PRE-CERTIFICATION
Developing prototypes for pre-certification and standard compliance involves meticulous adherence to regulatory requirements. These prototypes are rigorously tested to ensure they meet industry standards and safety regulations before formal certification. This eases the process of ensuring that products comply with legal requirements and are ready for market release.
-
3D PRINTING (PLASTICS)
3D printing is an additive manufacturing process that builds three-dimensional objects layer by layer from 3D computer generated designs. Its advantages include quick turnaround and geometry insight to designers, complex geometries that can be offer by other affordable prototyping processes, cost-effectiveness for low-volume production (when applicable).
IN HOUSE PRINTERS (PLASTICS)
Our staff and clients have at their disposal a fleet of 3D printing machines employing Stereolithography (SLA) and Fused Deposition Modeling (FDM) technologies. SLA creates high-resolution models from liquid resin, ideal for intricate designs and pre-manufacturing validation. FDM constructs objects by depositing layers of thermoplastic filament, offering durability and cost-efficiency, suitable for a wide range of applications and common in our CONCEPT stages.
MULTIPLE PROCESS AND MATERIALS (PLASTIC, CERAMICS & METAL)
While we have our own machines, we prioritize selecting the most suitable prototyping technology for each part. Understanding this, we've established partnerships with prototyping vendors. This ensures our clients receive optimal pricing and quality, irrespective of the process utilized, emphasizing our commitment to delivering superior results. Process and tailored methodology, backed by our expertise in various materials, including plastic, ceramics, and metal, enables us to cater to diverse prototyping needs efficiently.
SHOPWORK CRAFTING
Utilizing wood, cardboard, foam panels, foam core, plastic sheets, and off-the-shelf components, prototyping entails crafting low-fidelity models to explore concepts. These materials enable rapid iteration and experimentation, aiding in visualizing ideas, testing functionality, and refining designs before committing to more expensive production methods.
MACHINING (PLASTIC, CERAMICS & METAL)
Machining is a subtractive manufacturing process, where a CNC machine removes material from a solid block of plastic or metal to create a part based on a digital design. This process offers precision, versatility, and the ability to work with various materials, making it ideal for producing functional prototypes and low-volume production parts. In some cases it can be a better option than 3D printing.
RTV (PLASTIC)
The RTV (Room Temperature Vulcanization) process for plastic prototyping begins with creating a silicone mold from a master pattern. Liquid silicone is poured over the pattern, left to cure at room temperature, then removed, resulting in a mold suitable for casting multiple prototypes, mainly from urethane-based plastic. While the part price may be 5 to 10 times higher than plastic injection, the mold cost can be as low as 1/10 of injection molding tooling. This method is ideal for field testing units to be later injection molded or high-value, low-volume products not requiring mass production.
COMPRESSION MOULDING / OVERMOULDING
Compression molding for prototyping involves placing preheated material into a heated mold cavity. The mold closes, applying pressure to shape and cure the material. Yes... its exactly like making waffles*. After cooling, the part is removed. This method widely used at advanta for silicone prototyping and manufacturing, for electronic over moulding, low volume rubber parts.
*Just a friendly reminder: Please don't snack on compression-molded parts!RAPID TOOLING INJECTION MOULDING
Rapid tooling for injection molding incurs a higher cost due to expedited production, allowing parts to be obtained within two to three weeks post CAD approval. This automated process imposes constraints (sometime are a dealbreaker) that traditional vendors may not apply. Parts must adhere to standard injection molding practices without specific exceptions. While a range of off-the-shelf materials is available, exotic options are limited.
-
THERMAL ANALYSIS
We can take advantage of the 3D CAD of your product and material properties to simulate heat transfer and thermal behavior. By accurately predicting temperature distributions and thermal stresses, our designers and engineers optimize product designs to ensure thermal performance, reliability, and safety in real-world operating conditions.
MECHANICAL STRESS ANALYSIS
Developing prototypes for mechanical stress analysis entails using the modeled product components to simulate various loading conditions. Through Finite Element Analysis (FEA), designers evaluate structural integrity, identify potential failure points, and optimize designs to withstand mechanical stresses, ensuring product durability and reliability in service environments.
MOLD FLOW ANALYSIS
Mold flow analysis can be requested to manufacturer before miving to production. It involves simulating the flow of molten material within a mold cavity during injection molding. By predicting flow patterns, pressure distribution, and cooling rates, designers optimize mold designs to minimize defects, such as air traps and warping, ensuring high-quality plastic parts are produced efficiently and cost-effectively.
MANUFACTURING PROCESS
Our expert industrial designers possess a comprehensive understanding of manufacturing processes, spanning plastic, metal, and composite materials. Proficient in techniques such as plastic injection molding for intricate components, metal die-casting, CNC machining, and sheet metal manufacturing for robust parts, they excel in composite manufacturing, engineering lightweight yet durable products. With extensive field experience, Advanta seamlessly integrates innovative design concepts with practical manufacturing insights, ensuring products meet industry standards while accommodating complex assemblies.
-
Injection molding is a manufacturing process that is both complex and highly efficient. It involves injecting melted polymer into a mold to create parts that meet precise specifications. This process is widely used because it allows for the production of detailed and uniform parts in large quantities.
MATERIAL VERSATILITY
This process is versatile in terms of material selection, offering customization tailored to specific needs. The choice of material is crucial, as each type of plastic or elastomer has unique properties that must match the requirements of the part being manufactured. Each material has their technical advantages and disadvantages.
COST-EFFECTIVENESS AND AUTOMATION
Although the initial cost of mold fabrication is high, the cost per unit decreases significantly with large-scale production, making the process cost-effective for high quantities. Once the mold is created, parts can be produced rapidly. Additionally, the process can be automated, reducing labor costs and increasing production speed.
PRECISION AND OTHER BENEFITS
Injection molding is precise and repeatable, producing parts with tight tolerances and consistent quality. It allows for the creation of complex shapes that would be difficult, if not impossible, to achieve with other methods. The process generates minimal waste, as excess material can often be recycled and reused. Injection molding requires specific detailed design and precise control, but its economic advantages make it a valuable choice for the production of high-quality parts.
-
Elastomer overmolding, also known as rubber overmolding, is a manufacturing process where a layer of elastomeric material, such as rubber or silicone, is molded over a substrate or base material. This process creates a seamless bond between the elastomer and the substrate, enhancing the product's functionality, durability, and aesthetics.
Elastomer overmolding is commonly used to add soft-touch surfaces, improve grip, provide shock absorption, and enhance sealing properties in various products like tools, electronics, automotive components, and medical devices. It allows for the creation of complex shapes and designs, offering flexibility in product development and design optimization.
SOFT TOUCH AND TEXTURE OVERMOLDING
Overmolding can be employed to craft tactile details to enhance grip or even to bestow a premium appearance upon a product. By adding a soft layer, it enhances grip and provides a pleasant tactile sensation. This process elevates the product's allure by offering a comfortable and luxurious feel or a firm, non-slip grip to ensure it stays securely in hand.
PCB OVERMOLDING OR POTTING
Coating or encapsulation of printed circuit boards involves applying a protective layer of resin or epoxy over electronic components. This protects them from moisture, static propagation, dust, and other environmental factors. This process ensures durability and reliability in various applications, such as aerospace and automotive electronics.
OVERMOLDING OF SHOCK ABSORBERS AND BUMPERS
Overmolding to add shock absorbers and bumpers involves molding elastomer into specific shapes that provide shock absorption, vibration damping, and wall protection. This process enhances the durability and performance of the product in applications subjected to rough handling.
-
MACHINING (CNC)
CNC machining, or Computer Numerical Control machining, is a manufacturing process where computerized controls direct machine tools to remove material from a workpiece. This subtractive method allows for the production of intricate parts with precision and repeatability. CNC machining is widely used in various industries, from aerospace to automotive, due to its ability to produce high-quality components efficiently and accurately.
ROTATIONAL MOLDINGRotational moulding is a technique that involves filling a hollow mold with plastic powder, then rotating it to evenly distribute the material. After heating and cooling, this results in a hollow product without the need to assemble two separate pieces. Items such as kayaks, tanks, playground equipment, and swimming pool accessories can be manufactured using this process.
EXTRUSION-BLOW MOLDING
Extrusion-blow molding is a manufacturing technique where molten plastic is extruded to shape a hollow tube. This tube, still malleable, is then pinched into a mold, inflated, and cooled to produce a hollow product without the need for assembly. Common applications include the production of plastic bottles, containers, and conduits used in the automotive industry.
EXTRUSIONPlastic extrusion is a manufacturing process where thermoplastic material is melted and forced through a die to produce a continuous profile with a specific cross-sectional shape or pattern. This method is commonly used to manufacture products such as pipes, tubing, window frames, and plastic sheets for various applications.
VACCUME FORMING
Plastic vacuum forming involves heating a plastic sheet, stretching it over a mold, and shaping it using vacuum pressure. After cooling, the plastic maintains the mold's shape, yielding products such as packaging trays, smooth-surfaced plastic components, and signage.
OPEN MOLD COMPOSITE MOLDING
This manufacturing method involves manually applying resin and reinforcement materials onto an open mold. Layers are built up and cured in place on the mold to produce composite parts such as fiberglass boat hulls, automotive components, and architectural structures with excellent strength-to-weight ratios.
-
SAND CASTING
Metal sand casting is a process where molten metal is poured into a sand mold cavity. After solidification, the mold is broken, revealing the casting. Commonly used for producing intricate metal parts like engine blocks, gears, and artistic sculptures, sand casting offers versatility and cost-effectiveness in manufacturing.
DIE CASTING
Metal die casting involves injecting molten metal into a steel mold cavity under high pressure. Upon cooling, the mold is opened to reveal the solidified part. This process produces precise, complex metal components with tight tolerances and high surface finish, commonly used in automotive, aerospace, and consumer electronics industries.
PERMANENT MOLDS
Metal permanent mold manufacturing entails pouring molten metal into a reusable steel mold. It offers some advantages over die-casting in certain scenarios. While die-casting provides high production rates and tight tolerances, permanent mold casting offers lower tooling costs, longer tool life, and improved surface finish. It's ideal for medium to high-volume production runs and parts requiring high structural integrity.
-
MACHINING (CNC)
CNC machining, or Computer Numerical Control machining, is a manufacturing process where computerized controls direct machine tools to remove material from a workpiece. This subtractive method allows for the production of intricate parts with precision and repeatability. CNC machining is widely used in various industries, from aerospace to automotive, due to its ability to produce high-quality components efficiently and accurately.
SHEET METAL
Sheet metal manufacturing involves cutting, bending, and forming flat metal sheets into desired shapes and sizes. Processes include laser cutting, CNC punching, bending, welding, and assembly. Widely used in general, sheet metal fabrication produces various components such as panels, enclosures, and brackets.
CNC ROLLING
CNC rolling is a manufacturing process where metal sheets or strips are passed through rollers to achieve desired shapes or thicknesses. This process offers precision and repeatability in forming cylindrical or curved parts like pipes, tubes, and cylinders.
ALUMINUM EXTRUSION
The aluminum extrusion process involves heating aluminum billets and forcing them through a die to create complex profiles with consistent cross-sections. Products include window or door frames, curtain walls, and structural components for industries like furniture, transportation, and electronics, offering lightweight strength and corrosion resistance.
STAMPING
Metal stamping, akin to vacuum forming for plastics, involves pressing flat aluminum sheets between dies to form desired shapes with high force. This process yields lightweight, precise, and intricate parts from sheets, albeit at a higher cost due to die expenses. It enables the creation of complex surfaces with precision.
SALES & MARKETING TEAM SUPPORT
One lesson learned over time is that clients who have entrusted us with creating marketing materials for their products have more easily secured investments. We firmly believe that a development team responsible for both the mechanical and visual design of the product is better equipped to produce promotional imagery that highlights its best features. Our team ensures consistency, cohesion, and effective communication of the product's value across different formats.
-
QUICK CONCEPTS
In the dynamic landscape of product development, quick, stunning visual sketches serve as the catalyst for setting the tone of our future product line. With their persuasive charm, they ignite imagination, convey concepts with clarity, and inspire confidence, laying the foundation for a compelling and successful brand narrative
PHOTOREALISTIC RENDERINGS OF PRELIMINARY CAD
Photorealistic rendering offers a shared vision for the engineering team and marketing group. By presenting lifelike representations of upcoming products, it fuels excitement, generates interest, and aligns stakeholders on design direction. This immersive experience fosters collaboration and empowers teams to deliver innovative solutions that captivate and delight customers as well as setting the design intent for whom will work on the project.
TRADE SHOW EARLY PROTOTYPE
Physical trade show prototypes, resembling the final product, create tangible experiences for potential customers. They offer a firsthand glimpse into product features and benefits, generating excitement and fostering early sales inquiries. By showcasing the product's potential, these prototypes drive anticipation and lay the groundwork for future sales success.
HIGH QUALITY CUSTOM DIGITAL PRESENTATION MATERIAL
Advanta Design excels in crafting captivating presentation documents to generate hype internally and externally. Images, custom presentations or animations, these documents can showcase your project highlights, product features, and benefits with stunning visuals and compelling narratives. Whether for internal divisions or sales teams at tradeshows, our materials effectively communicate the product's value proposition, igniting excitement and driving sales.
-
PHOTOREALISTIC RENDERINGS FOR MARKETING
Photorealistic renderings enable the creation of digital images beyond the constraints of regular photography. By digitally crafting environments, products, and scenarios, renderings offer unparalleled flexibility and creative freedom. This allows for the visualization of concepts and ideas that would be challenging or impossible to capture with traditional photography such as exploded views, see trough enclosure, multiple products showed in the exact same viewing angle.
DIGITAL ANIMATIONS
Dynamic video digital animation is a versatile tool for crafting captivating marketing and training content that fuels sales growth and positive feedback from users. By animating products with engaging visuals and motion, it captures attention, effectively conveys key messages and functions.
BROCHURE & PRINTED MATERIALS
With a deep understanding of your product's form and function, we're uniquely positioned to create compelling brochures and printed materials. Our intimate knowledge allows us to showcase its features effectively, producing stunning printed and digital materials that effectively communicate its value.
TRADE SHOW BOOTH / BACKDROP AND POP UP
Our firsthand experience with the materials developed for your project, coupled with our in-depth knowledge of your company's marketing brand guidelines and graphic design proficiency, positions us as an ideal partner for crafting captivating tradeshow booths and roll-ups. This comprehensive approach guarantees cohesive branding and visually striking displays that effectively engage our audience.
LOGO DESIGN AND BRANDING
Harnessing our creative graphic design expertise, we craft innovative and targeted logos for your product and your company. With an in-depth understanding of your products an your business personality, we infuse creativity from an external perspective, ensuring logos and your brand effectively communicate your message to your audience.
-
UNPACKAGING AND USER EXPERIENCE
Unpackaging and package design are crucial for user experience, ensuring products are handled and protected appropriately. Thoughtful design enhances usability, protection, and presentation, instilling confidence and delight in customers. It communicates care for the product, enhancing brand perception and fostering positive interactions with users.
OFF THE SHELF TRANSPORT SOLUTIONS
With extensive expertise, our team aid clients in choosing and tailoring off-the-shelf carrying solutions for premium field-deployable products. Our personalized approach guarantees optimal fit and protection, enhancing both portability and durability. We excel in elevating off-the-shelf items to a customized appearance and functionality, delivering superior results.
IN-STORE PACKAGING, BLISTER PACK, IN-STORE PRESENTATION
Advanta guides clients through the complexities related to product presentation in stores, packaging, and blister packs for consumer products sold on shelves. Leveraging our expertise, we create cohesive solutions that enhance your brand's visibility, stimulate product engagement, and optimize shelf appeal, promoting its success in the competitive retail landscape.
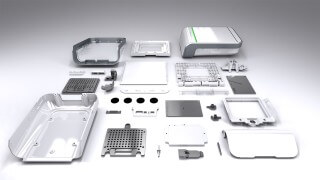
OUR DEVELOPMENT PROCESS
Our team has developed a unique process and tailored methodology , focusing on mechanical product development rather than software tracking or event creation. This approach enables us to define relevant checkpoints and enhance the accuracy of our deliverable evaluations. We meticulously track our design efforts and incorporate them into our comprehensive project database. This helps assess project timelines and efforts at predefined stages. Our skilled design team strives to provide you with a seamless project progression, while our project managers and sales teams use this data to make informed budgetary comparisons and forecasts to plan for future required investments.
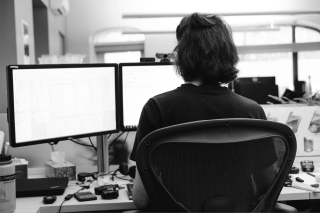
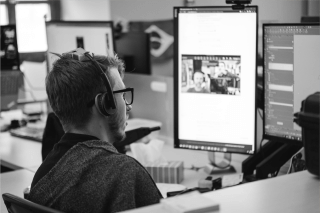
OPPORTUNITY
As industrial designers, we assist clients in navigating the Opportunity Stage, yet it's crucial to recognize that clients frequently undergo preliminary stages independently. Typically, clients engage in idea generation, opportunity scouting, and feasibility research autonomously before seeking our expertise. They explore possibilities, make initial concepts, and outline rough functionalities, embodying the essence of their innovation.
However, our role extends to enhancing their efforts by incorporating creativity, technical proficiency, and strategic insights into the design process. Upon request, we can engage in these early stages where the vision and objectives for the new product have yet to be fully outlined.
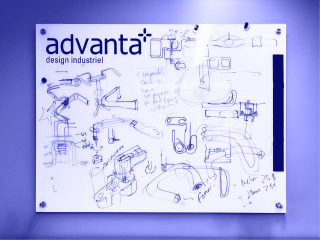
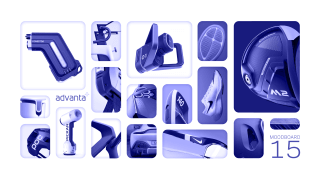
STRATEGY
In the Strategy Stage, our primary objectives are to understand your innovative ideas, scout for promising opportunities, and conduct feasibility research to ensure practicality.
We familiarize ourselves with your brand, define and refine product requirements, conduct competitive research and identify key differentiators.
Mood boards and personality boards help shape the product's aesthetic and branding differentiation, while personas and journey maps provide insights into user experiences and potential features to focus on. Through these steps, we lay a solid foundation for a successful design process, ensuring alignment with your vision and market needs.
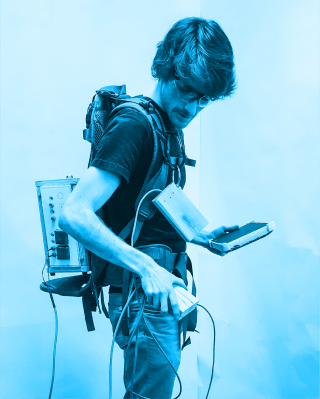
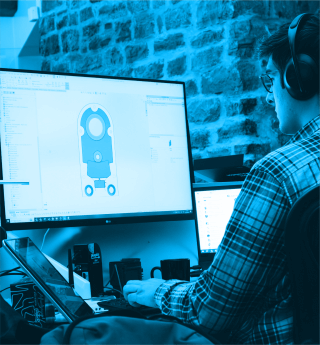
TECHNICAL CONCEPTS
At the technical concept stage, our objectives revolve around practicality and feasibility. We explore concepts, evaluating their viability. We establish potential mechanical frameworks and delve into initial CAD explorations to visualize the concepts. We integrate predefined components and explore various usage and assembly scenarios. The initial prototypes (P0) allow us to validate our ideas, ensuring that functionality and ergonomics align with your expectations in terms of volume, user experience, and ergonomics.
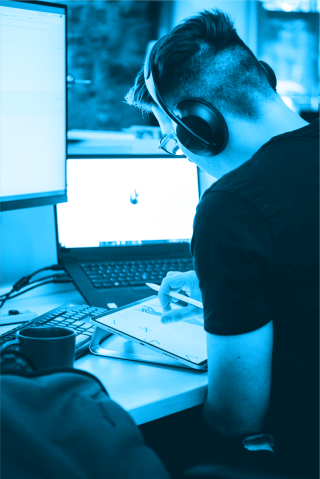
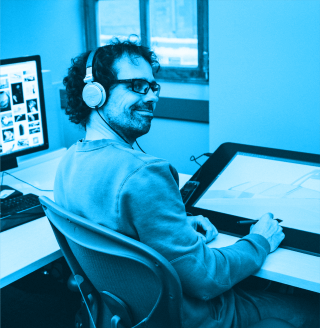
VISUAL CONCEPTS
Visual design sketches breathe life into concepts, allowing us to iterate and refine designs effectively. The Concept Stage is where ideas transition into tangible frameworks, setting the stage for further development and refinement.
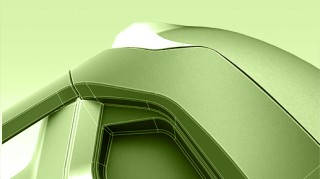
REFINEMENT
In the Refinement Stage, our focus shifts to refining ideas and layouts. We meticulously refine component layouts, ensuring optimal functionality and integration.
Surface CAD models and volumetric physical models provide tangible representations for evaluation and validation. Photorealistic renderings help bringing your idea in to the world, offering a glimpse into the final product's aesthetics and appeal. This stage is where ideas evolve into tangible forms, allowing for thorough assessment and refinement before moving forward in the design for manufacturing stages.
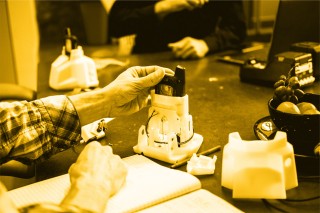
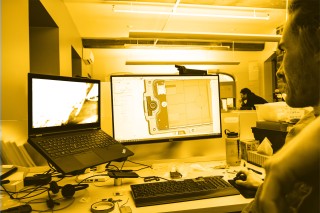
development
In the Development phase, our goals revolve around practical execution and validation. CAD models are developed, focusing on mechanical resolution for seamless integration. Prototypes (P1) are created to check and validate ideas in a concrete context, confirming both the ergonomics, aesthetics, and functionality of the product. Progression in the project during this phase usually allows for a good assessment of production costs as well as suitable manufacturing partners.
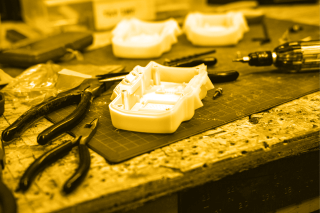
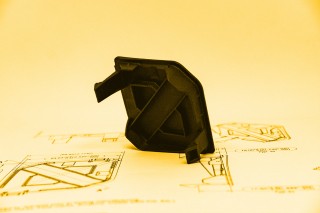
We meticulously assess and confirm the usability and pragmatism of the product while considering financial objectives to ensure consistency with budgetary constraints. We explore various manufacturing options and suppliers to ensure optimal production efficiency. The development phase is where ideas are sufficiently developed to be subjected to reality, undergoing rigorous testing and validation to ensure they meet functional, budgetary, and aesthetic requirements.
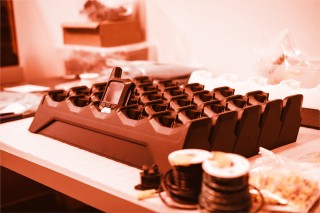
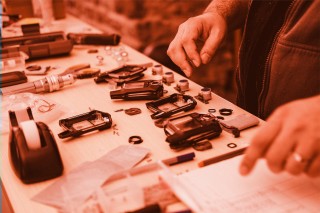
DETAILING
In the Detailing phase, our focus is on optimizing manufacturing processes and profitability. We assist you in carefully selecting the right partners from among the options presented to you in the previous phase.
We actively participate in discussions with these partners to streamline the design so that it is optimal for production with the partner you have chosen. Cost optimization is prioritized to align with budget constraints without compromising quality. Details are refined, incorporating specific adjustments necessary for manufacturing feasibility.
Prototypes (P2) are finalized and validated to ensure they meet design specifications. Comprehensive manufacturing documentation is prepared to effectively guide production processes. The Detailing phase ensures that every aspect of the design has been meticulously examined and optimized for smooth manufacturing, ensuring successful realization of the product and your confidence in the investment required to start production.
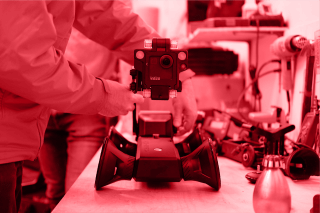
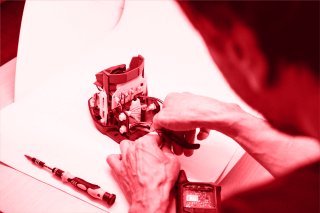
PRODUCTION
In the Production phase, your product is manufactured for the first time. We validate the parts, their precision, and assess the quality of the assemblies. We must give the same rigor to quality control as was given to the design. The quality of the product should reflect the intelligence of its design, maintaining high standards.
Mechanical tests are conducted to verify the performance and durability of the product. Minor adjustments are made to the parts if necessary to address any unforeseen issues and optimize product performance. Tooling adjustments are made if necessary. Assembly jig creation is done to improve the efficiency and precision of assemblies in production.
Throughout this phase, we provide continuous support to ensure smooth production implementation for you. This phase is the final barrier before your product is officially in the hands of a customer.
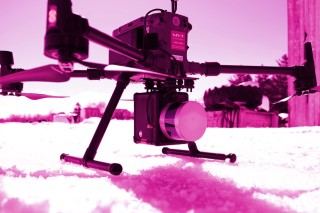
PRODUCT LAUNCH
During the Product Launch phase, our focus shifts towards creating impactful marketing materials that highlight the features and benefits of the product. We develop concise content that effectively communicates the key selling points, thereby attracting potential customers. Images are carefully crafted to captivate the audience and spark interest in the product, showcasing its functionality and appeal. Renderings and animations provide realistic representations, immersing the audience in the product experience.
This phase serves as a platform to effectively leverage your creative assets, communicating the product's value proposition to generate excitement and drive sales. Since these activities typically occur in the later stages of projects, it sometimes necessitates producing materials earlier than production. This early preparation usually supports product launch in crowdfunding campaigns, aids in stimulating funding rounds, or assists in internal progress report presentations.
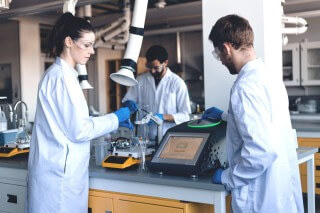
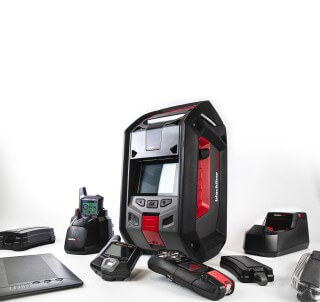
PRODUCT LIFE
Throughout the lifecycle of your product, it may be necessary to adapt to new circumstances and evolving criteria. Technological upgrades may also be necessary to meet changing market demands. We offer support to improve your existing products and rejuvenate old ones. Additionally, expanding product ranges and developing accessories can be long-term strategies to meet diverse consumer needs. Cost reduction efforts can ensure sustainable competitiveness without compromising quality.