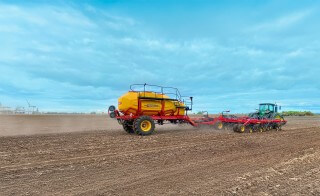
REAL DESIGN
BUILT TO ENDURE
A NEW PROCESS
FOR A NEW MARKET
This project aimed to support the engineering team at Väderstad Saskatchewan, which specializes in designing seeding and field preparation equipment. The task was to develop a smaller air cart for European markets, utilizing plastic bins instead of traditional welded sheet metal containers. Since their expertise lies in engineering and designing metal equipment, they enlisted Advanta's help. Advanta provided support in the visual design, ergonomics, and assembly logistics of the new air cart, as well as in the technical design of the plastic enclosures.
GAINING INSIGHT
TROUGH EXPERIENCE
When designing a new product, it’s essential to immerse yourself in the experience and engage with the people who use, assemble, or manufacture it. We needed a deeper understanding of how the product is used, cleaned, how it ages over time, how it is assembled, stored, and, most importantly, how it is manufactured and what the local manufacturing capabilities are. By visiting the site and meeting these stakeholders, we were able to design a product that meets the needs of everyone involved in the project.
DIFFERIENCIATION
TROUGH CONCEPTS
Using the initial technical models, we created multiple rounds of sketches to explore what the product could become, guided by an understanding of the available manufacturing processes. This approach allowed us to present plausible and technically accurate concept designs. The sketches were shared with the client, who selected their favorite—often combining the best features from multiple concepts into a single, refined design.
AN HEAVY LOAD
OF PRECISION
When modeling the product, we had to account for specific internal volumes, as each container had a unique capacity for grain or liquid fertilizer. These containers were mounted on load cells to enable real-time tracking of their contents, which added complexity since different grains vary in size—meaning the same weight could represent different seed volumes. Additionally, as the cart moves through fields and roads, ensuring the stability and safety of the bin structure was critical. Collaborating closely with the engineering team at Väderstad, we successfully completed the design of the bin cradles to meet these challenges.
INDEPENDENCE
AND CONTINUITY
After delivering the manufacturing files for the plastic components, the engineering team at Väderstad took over the design of the product's structure and surroundings, staying true to the initial sketches and concepts. They did an excellent job, creating a functional, structurally sound, and ergonomic product.
Pleased with our work, they asked us to collaborate on their next air cart project, which we jumped into right away.